More and more companies are using recycling to achieve their sustainability goals. This means that the demand for remanufactured rolling bearings is increasing.
– This has enormous potential, says Hannes Leopoldseder, head of SKF’s remanufacturing center in Steyr, Austria.
The wind power industry is an industry that has recently started turning to SKF for the remanufacturing of turbine bearings. A change that is easy to understand given the industry’s focus on sustainability in terms of products.
– Although the industry has used remanufactured components such as electronics and sheet metal for many years, the use of remanufactured rolling bearings has lagged behind. But now wind turbines have evolved, gotten bigger and increased in lifespan, so remanufactured bearings have become more interesting.
Also large in the steel industry
SKF has worked with a steel manufacturer for over 10 years, remanufacturing over 39,000 bearings used in continuous casting machines (CCM). It has helped the company reduce CO2 emissions by more than 65 tons per year and led to zero equipment failures due to the bearings. In addition, annual CCM inventory costs have decreased by an average of approximately $500,000.
Another steel company wanted to reduce its CO2 emissions by a third. To succeed, they looked at the processes that generate the largest emissions, for example blast furnaces. However, the company focuses on reducing emissions wherever possible. Machines that cast slabs require around 2000 new ball bearings per year. By remanufacturing half of these, 10 tons of steel and approximately 62,000 kWh of energy are saved every year, while eliminating almost 30 tons of CO2 emissions.
To achieve savings, remanufacturing must be integrated into the company’s operational maintenance plans. Identifying the best time to remanufacture a stock is critical to success. It must not be too worn, but must be replaced at a level of wear that allows the bearing to be remanufactured to new condition. There, Leopoldseder sees great potential in surveillance and artificial intelligence to find the right balance.
Two units for remanufacturing in Sweden
Hannes Leopoldseder works at one of SKF’s more than fifteen global centers for the remanufacturing of rolling bearings. He says there is a trend in some industries more than others to reuse inventory.
– But in almost all cases it tends to be the manufacturers or operators where the sustainability goals are already at the top of the agenda and who act the fastest.
Stock remanufacturing is a method that is gaining ground. Today, SKF can remanufacture most bearings. To expand capacity in Sweden, there are two units, one in Gothenburg and one newly opened in Kiruna. Local units that enable circular solutions close to customers.
Demand for the unit in Gothenburg increased by four times in just two years.
“Reduce, Reuse, Recycle”
More and more standards are being introduced by global and national governing bodies to improve manufacturer sustainability. Something that accelerates the use of remanufactured rolling bearings. However, says Leopoldseder, it must be a joint movement, based not only on standards but also on customer demand for more sustainable alternatives.
– Buyers consider not only whether a product is manufactured in a sustainable way, but also whether at the end of its life there is a sustainable method of waste management and whether its components can be reused. A way of thinking that will take us from a linear economy based on “take, make and consume”, to a circular one based on “reduce, reuse and recycle”.
SKF looks ahead
If we look ahead, Leopoldseder believes that the automotive industry is a good example to start from.
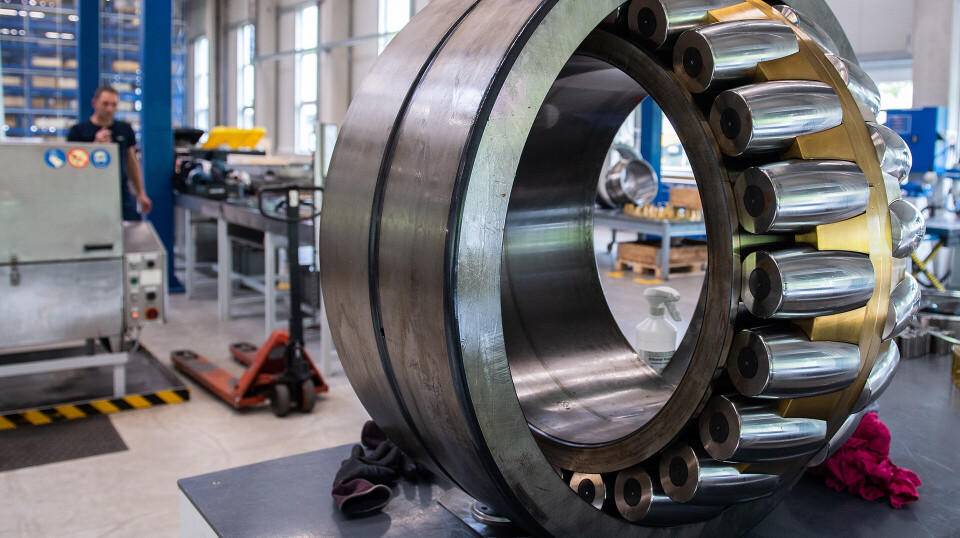
– When a truck engine needs to be replaced, the buyer will look for a remanufactured one – without asking questions about quality or whether the engine is new. The “new” engine has been built from parts from several different vehicles spread all over the world. SKF remanufactures a customer’s own bearing which is then shipped back to them. If remanufactured stock was a “product”. Just like truck engines, costs would potentially be lower, while shortening lead times. It is one of the main original driving forces behind remanufacturing.
Source: www.nyteknik.se