The mining it’s a sector still very pollutingso solutions have been tested for some time now with electric trucksThe problem is the batteries, which have to be huge to power the wheeled giants that operate in the mines, such as dump trucks.
This means extra weight that hinders their work, since they have to transport the material. On the other hand, there is the problem of autonomy: if they need to be charged, they are inactive for hours. Thus, several solutions have been proposed, such as battery exchange. And now, too, An old concept is being tested: the trolleybus.
An electric mass that recharges while working
This is what this one is doing huge electric dump truck from Hitachi Construction Machinery, which has been signing since June First feasibility test of a fully battery-powered vehicle in a real-world setting: First Quantum Minerals’ massive Kansanshi copper-gold mine in Zambia. The two companies have partnered to reduce emissions at their mines.
Based on an EH 4000 AC-3 dumperhas replaced its gigantic 16-cylinder Cummins diesel with an electric system for which they have collaborated with the technology company ABB electrification systems specialist. Its battery is powered by a catenary circuit.in combination with a regenerative braking system.
Thus, on slopes, when energy is most required, the battery is connected to the elevated electrical circuit thanks to its pantograph. On the descent into the mine, it regenerates the battery to have sufficient energy available for filling up in the mine. And after leaving the mine, it starts again.
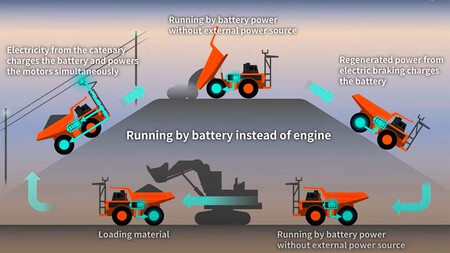
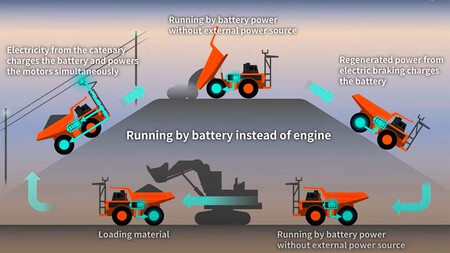
This cycle and the way the truck works is precisely what is being tested at this mine in Zambia: to verify the loading and unloading cycles, as well as the performance of the truck with real loads when travelling, turning and stopping.
Using a catenary-based system allows the battery size to be reduced and thus be able to take on a larger transport load, to get as close to that of a diesel truck as possible and be as productive as possible. This type of dumper, if electric, requires huge battery packs: the battery packs of this eDumper were 4.5 tonnes for 600 kWh of capacity.
The EH AC-3 surpasses this eDumper in dimensions: in this version It is over 14 m long and 7.0 m high, with a weight of 163 tons.. This would require even larger batteries. In any case, Hitachi does not specify the size of the battery in this dump truck or its capacity.
Also the need to recharge the battery is eliminated, since it does so while workingas well as increasing their life cycle, according to their creators. Added to this are lower costs: batteries remain the most expensive components in electric vehicles.
More useful in mining than in road transport. Using catenaries is something that has also been tried with electric road transport trucks to save loads and to be able to transport goods without stopping. But they are not viable due to the enormous infrastructure they require.
In these tests, For 40 km, an investment of 190 million euros was needed. An amount that did not compensate for the emissions saved compared to diesel-powered trucks: in the best case, a maximum of 22%.
But in mining, the catenary circuit is smaller, even more so if they are only installed at critical points such as uphill slopes. First Quatum points out that it already has part of the infrastructure needed for these dump trucks with full batteries, so the investment is smaller. If it turns out to be viable, it will be an important step towards green mining.
Source: www.motorpasion.com