In 2008, when Verkhnyaya Chona produced its first commercial oil, it was assumed that the field would be developed within 20-30 years. Now VCNG is making plans until the middle of the century. Indeed, in terms of hydrocarbon reserves, constantly increasing both due to new drilling and thanks to modern interpretation of seismic data, the Verkhnechonskoye field this year moved from the category of large to unique. In just nine months of 2024, its reserves increased by 19 million tons of oil – this is almost three times the average annual production.
– Today we have a business plan for five years and long-term plans for twenty years. They are periodically adjusted, including because technology does not stand still, solutions are constantly emerging that make it possible to increase the life cycle of a field and to reach the production of oil that could not have been thought of before. Let’s say, 30 years ago the Verkhnechonskoye field was considered unprofitable. And last year we produced the 100 millionth ton of oil,” says Vadim Tsuker, General Director of Verkhnechonskneftegaz JSC.
Higher, deeper, wider
At the end of last year, VCNG began full-scale development of the Preobrazhensky horizon. It is located at a depth of 1600 meters, above the Verkhnechonsky horizon, which the company is currently developing. However, Preobrazhensky has its own specific structure, and therefore requires special extraction technologies. Verkhnechonskneftegaz specialists proposed a horizontal drilling method with penetration of a productive formation of 1000 meters and subsequent nine-stage hydraulic fracturing (HF).
– Currently, 23 wells have been drilled: 21 production and two injection wells (with their help, produced water is pumped in to maintain pressure in the formation. – Ed.). In the future, we plan to further full-scale drilling of the Preobrazhensky horizon. This process is not fast, it will take several decades,” explains Nikolai Vedernikov, Deputy General Director and Chief Geologist of Verkhnechonskneftegaz JSC.
In addition, the commercial oil content of the Ust-Kut horizons, which lie even higher, has been proven – this is a prospect for the near future. In the meantime, the company continues to develop the lower – main – horizon. And this can be considered the answer to the question of how long they intend to develop the field.
In addition to the construction of new well pads, an infill drilling program has been operating at the Verkhnechonskoye field since 2019. Additional wells are being installed in already developed areas in order to bring into production areas of the oil-bearing reservoir that are not covered by the existing well stock. During this time, 117 wells were put into operation, which provided more than 2.6 million tons of additional production. Their starting flow rate was almost one and a half times higher than planned and reached 70 tons per day.
Along a new trajectory
To maintain production levels, the company is introducing new advanced methods of drilling, equipping wells and maintaining pressure in the rock. You will no longer surprise anyone with horizontal drilling – today there are more than 700 such wells on the Upper Chon.
– The thickness of the oil-bearing formation that we are developing is 10-15 meters. If we drill vertically, then we will open it only to these 10-15 meters, if horizontally, then to 1000-2000 meters. The flow rate of such a well will be much greater. And considering that there can be 5-7 such wells, with multi-directional horizontal reservoirs, we cover an area of the oil-bearing formation with a diameter of approximately five kilometers,” explains Viktor Nikitenko, Deputy General Director for Drilling at Verkhnechonskneftegaz JSC.
Any employee can come up with an improvement proposal and issue a production efficiency passport. The idea will be reviewed by experts. Photo: Ekaterina Dementieva
Another method is multilateral wells, in which several additional side branches extend from a horizontal wellbore. Rosneft drillers have complicated the well-known design by increasing the number of sidetracks. The well was named “Birch Leaf” – for its resemblance to a tree leaf. It has a large length of penetration through the collector. There are already 50 of them in the VCNG fund. In this way, not one, but three to four thousand meters of the reservoir are opened. Oil recovery, accordingly, increases significantly.
– Since 2016, we have also been using horizontal sidetracking – this, on the one hand, helps to revive wells whose flow rate has decreased, and even cover overlying horizons with their help, and on the other hand, to obtain serious savings. There is no need to develop a well from scratch – you can use the existing infrastructure, a ready-made shaft, drill an inclined reservoir from its upper part and reach the desired point. At the same time, costs for additional equipment and consumables are reduced. To date, VCNG has already given a second life to 14 wells in this way,” points out Nikolai Vedernikov.
The construction of wells with complex trajectories requires special drilling fluids. At the Verkhnechonskoye field, a hydrocarbon-based solution has been used for several years, the main component of which is Rosneft’s own synthetic oil. Recently, Verkhnechonskneftegaz specialists introduced a new composition: an emulsion with an oil-to-water ratio of 30:70. Its advantage is to reduce the volume of hydrocarbon base and the cost of drilling. The technical parameters of construction are maintained. The economic effect averaged 20 percent per well.
Every year, VChNG oil workers improve their hydraulic fracturing technologies. Here it is necessary to clarify that oil does not lie underground in lakes – it saturates rocks, like water saturates a sponge. When drilling, oil under pressure from overlying formations begins to ooze from the pores into the well. But the impact of different breeds is very different. The dense sandstones of the Verkhnechonskoye field require additional measures, such as hydraulic fracturing. To do this, a special liquid is supplied into the well under high pressure, which forms deep cracks in the oil-bearing formation. To prevent them from collapsing, bulk material is pumped into them – proppant (tiny ceramic balls) with a high oil recovery factor. The specifics of the operation are developed individually for each well.
Import substitution took place
It was generally accepted that advanced technologies in oil production could only be used with imported equipment. However, time has shown that this is not the case. According to Vadim Zucker, a wide range of installations, components and consumables are today supplied by domestic manufacturers. Oil industry workers are satisfied with the quality of their products.
– Every month there are more and more Russian companies that produce this or that equipment we need. I can clearly feel this in procurement: if previously one Russian participant would go to auction, today two or three are competing for the same lot. Import substitution is growing exponentially, and I think we can say that it has taken place,” emphasizes the general director of VCNG.
A striking example is a robotic manipulator for connecting drill pipe joints during tripping operations at wells. Both the robot itself and the program for it are Russian. Today, all echelon-type drilling rigs operating at the Verkhnechonskoye and Severo-Danilovskoye oil, gas and condensate fields are equipped with them.
– Previously, we used hydraulic wrenches: workers had to manually bring in such a wrench, secure it to the column, then unfasten it and move it away. This required a lot of physical effort and took time. The robotic arm connects each pipe in just 31 seconds – twice as fast as humans. He comes up on his own, loosens the connection of the drilling tool himself, attaches the next “candle” himself, moves away on his own – the operator just needs to press a button,” says VCNG drilling supervisor Denis Kravchuk.
Considering that 145 connections and disconnections of pipes are required to lower a column into a well 3.5 kilometers deep, the time saved for drilling each shaft is 10 hours. This allows you to optimize the drilling process, which is already brought to a high level of automation. If in the 80s of the last century, under similar geological conditions, a well would have been drilled for a year, at the beginning of the current century – more than a month, but today specialists can complete it in an average of 22 days.
Another example is the Russian automated directional drilling control system, which was implemented at Verkhnyaya Chona and the fields of the Danilovsky cluster.
Complex drilling trajectories require highly skilled and focused operators. The implemented automated control system is a person’s faithful assistant. The program accurately maintains the specified drilling parameters, helps to compensate for geological difficulties, increase the mechanical speed of penetration, the length of the horizontal section of the trunk, and at the same time reduce the construction time of wells by two days.
– The program, for example, allows, if necessary, to turn off the rotary engine – leave it together with the bit motionless (so as not to change the drilling trajectory), and only rotate the string due to the top drive. And vice versa. This helps reduce production risks, equipment wear, and drilling fluid consumption,” explains VCNG drilling supervisor Alexander Kalchenko about the development possibilities.
By the way, as the rig workers point out, the top drive is an example of production localization. Previously, such equipment was produced by a German company entirely from imported components. The drive that works at the field today is made in Russia.
Rosneft has found resources to increase operational efficiency within the company. Our own technicians perform various types of repairs on complex equipment within a few days. And employee innovation proposals can save millions of rubles.
– Any company employee can come up with an improvement proposal and issue a production efficiency passport. The idea will be reviewed by experts, they will evaluate its economic efficiency, and if approved, the proposed practice will be replicated. “Rosneft receives over a thousand such proposals a year, and VCNG receives about 75. These are excellent innovative ideas that we draw from our employees,” says Vadim Tsuker.
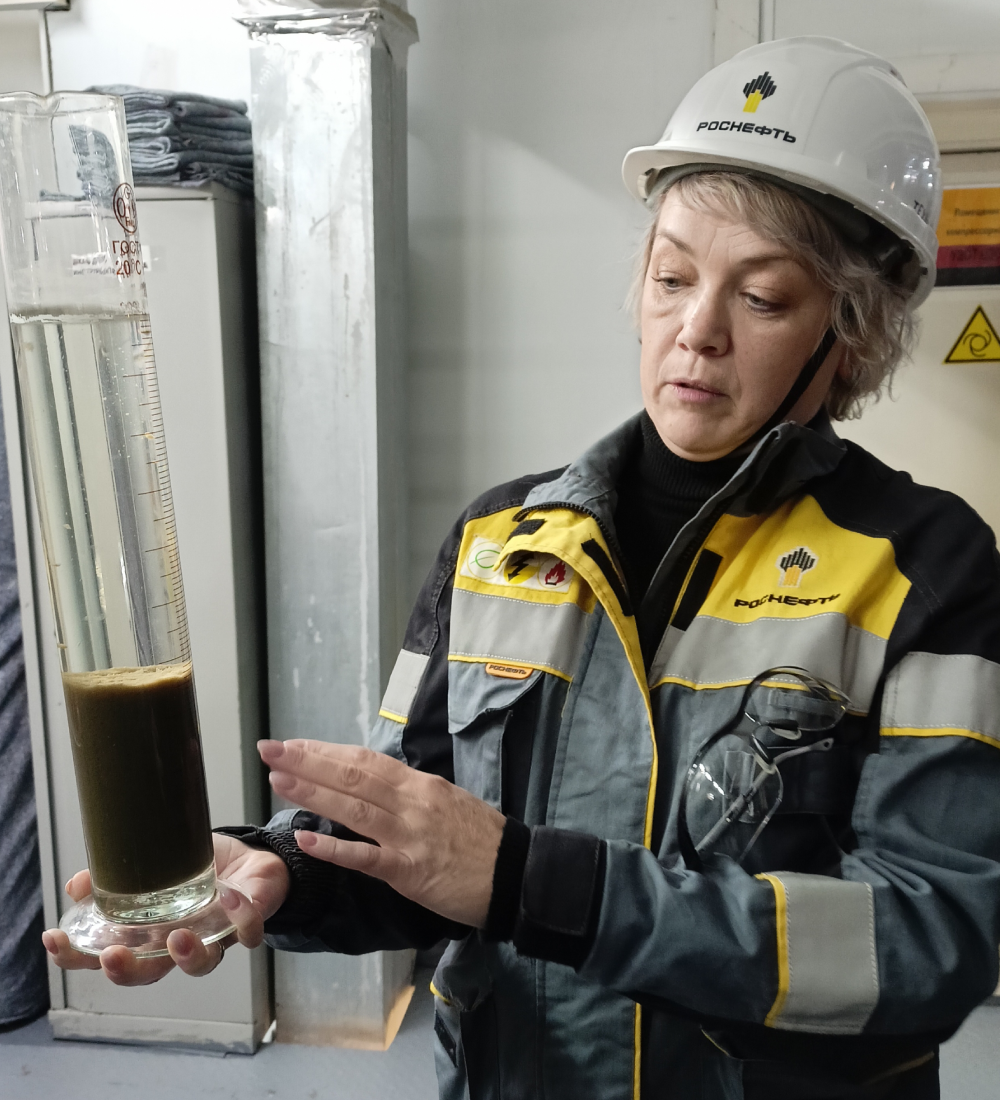
The company found internal resources to improve operational efficiency. Photo: Ekaterina Dementieva
Help “RG”
JSC Verkhnechonskneftegaz is developing the Verkhnechonskoye oil and gas condensate field, one of the largest in Eastern Siberia, which is located in the Katangsky district of the Irkutsk region. The company is also the operator of work at the licensed areas of Rosneft in the Irkutsk region and Krasnoyarsk region.
Source: rg.ru