Circularity is a central aspect of society’s sustainable transformation, which places increased demands on efficient resource consumption and climate-friendly production. The development means new challenges for the industry and it is becoming increasingly important for companies to reevaluate their processes. To promote a circular industry, SKF works to develop new technical solutions.
In collaboration with Ovako and Stena Recycling, SKF runs a production chain that aims to reduce the amount of production waste. Ovako manufactures steel which is delivered to SKF where it becomes rolling bearings, during production Stena Recycling collects the production waste which is sorted and quality assured on site before it is returned to Ovako to be melted down into new special steel. From the collaboration, a circular value chain blossoms where maximum benefit can be extracted from the resources.
– Through the collaboration, we have reduced our climate footprint, which has contributed to the fact that today we have net zero emissions in our production unit in Gothenburg, says Johan Wiksfors, Key Account Manager, Reliability Engineering at SKF.
Joint forces give life to circular processes
The project shows how residual products can be recycled and returned to production in a circular process. The collaboration, which has been going on for a long time, has been gradually optimized based on a common ambition to reduce the industry’s climate footprint. Today, SKF can recycle close to 100 percent of all grinding chips and grinding dust and over 90 percent of production scrap.
– For us, it simply means utilizing our resources in a better way and ultimately reducing our need for new steel, says Johan Wiksfors.
Ovako is one of Europe’s leading manufacturers of component steel. Mikael Bror, purchasing manager of raw materials at Black Bar, says that circularity is an important part of the business. Every year, around 2,500 tons of residual products from SKF are recycled and turned into new special steel at Ovako.
For a sustainable steel industry
In order for the steel to go directly into the furnaces and be melted down, the return material must be delivered well sorted. Thanks to Ovako manufacturing the steel itself, the production chain has been designed for as efficient a process as possible.
– The advantage is that the recycled steel is a known material for us, we have manufactured it ourselves. If it arrives sorted, we can immediately return it to new special steel, says Mikael Bror.
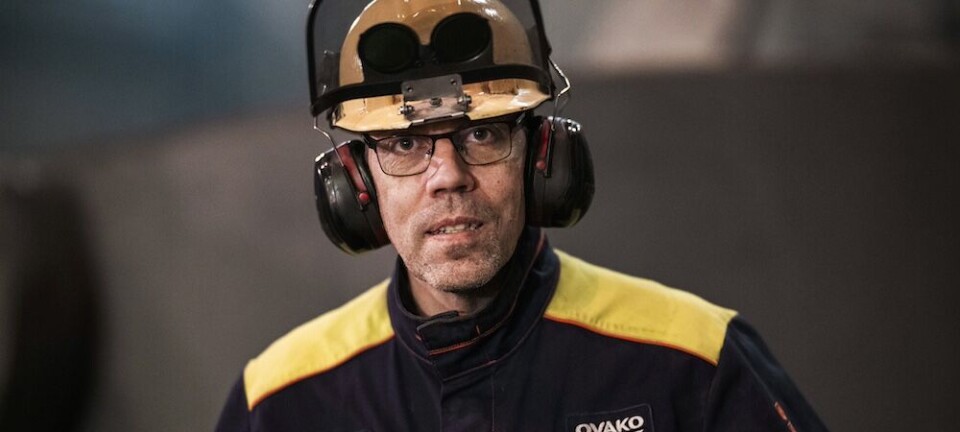
The circular value chain has been shown to generate several positive effects. The collaboration not only contributes to a reduced need for primary alloys and increased economic benefits, it also brings great profits from a market and sustainability perspective.
– In the future, there is hopefully no end customer who wants to buy steel from a producer with a high environmental impact, I think everyone wants to take responsibility and protect the planet, says Mikael Bror.
Today, Ovako is the steel producer with the lowest carbon footprint in Europe and the journey continues with new investments in renewable energy sources. At the company’s newly inaugurated facility in Hofors, the steel is heated with fossil-free hydrogen gas. An important step to enable carbon dioxide-neutral steel production.
– We have done it in two stages, where we first converted our production from heating oil to propane, now we are going from propane to hydrogen, says Mikael Bror.
The bridge between SKF and Ovako
As an important link between SKF and Ovako, Stena Recycling ties the production chain together into a single efficient flow. Today, Stena Recycling has overall responsibility for SKF’s waste solutions. A work based on sorting as close to the source as possible and direct reuse of materials. The method means that Stena Recycling spends a lot of time at the customer’s place to collect and sort materials on site where production takes place.
– We collect, sort and quality-assure the material with various analysis tools in order to deliver the right quality of steel to Ovako, says Fredrik Lyckesvärd, who is business area manager for iron and stainless steel at Stena Recycling, and continues:
– Our long experience and high competence in recycling, together with our ability to deliver process-critical raw materials, means that we can help our customers with solutions that accelerate the circular transition. There is now a huge demand for smart circular solutions.
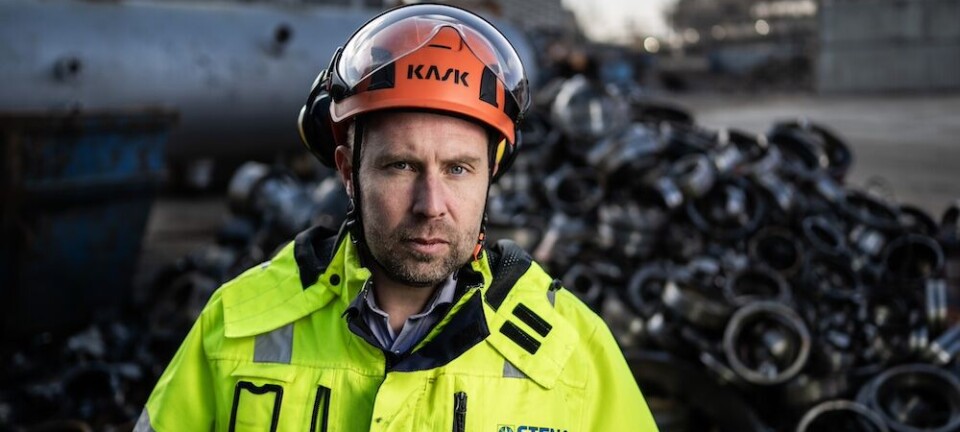
In addition to recycling, Stena Recycling also supports its customers in the development towards sustainable business models.
– Cooperation is a strength when it comes to solutions, through our understanding of the customer’s needs, we can put these into practice in the best way in the value chain, concludes Fredrik Lyckesvärd.
Read more about SKF’s work for a sustainable steel industry.
Source: www.nyteknik.se